Welding WPS: Usual Errors to Prevent and How to Correct Them
Welding WPS: Usual Errors to Prevent and How to Correct Them
Blog Article
Unlocking the Power of Welding WPS: Techniques for Effectiveness and Security in Construction
In the realm of fabrication, Welding Treatment Specs (WPS) stand as the foundation of welding procedures, determining the needed steps for achieving both efficiency and safety in the manufacture procedure. Recognizing the ins and outs of WPS is vital to utilizing its full potential, yet several companies have a hard time to unlock the true power that exists within these records (welding WPS). By diving into the strategies that maximize welding WPS, a globe of improved productivity and heightened safety and security waits for those prepared to explore the subtleties of this crucial aspect of fabrication

Value of Welding WPS
The significance of Welding Treatment Requirements (WPS) in the fabrication market can not be overemphasized. WPS serve as a crucial roadmap that lays out the necessary steps to make sure welds are executed constantly and correctly. By specifying important specifications such as welding procedures, materials, joint layouts, preheat temperature levels, interpass temperatures, filler metals, and post-weld heat treatment demands, WPS give a standardized method to welding that improves effectiveness, top quality, and safety and security in construction procedures.
Adherence to WPS assists in attaining uniformity in weld top quality, decreasing the possibility of defects or structural failures. This standardization also facilitates conformity with sector policies and codes, making certain that produced frameworks meet the called for safety and security criteria. In addition, WPS documentation allows welders to replicate successful welding treatments, leading to constant outcomes across different projects.
In essence, the careful growth and strict adherence to Welding Procedure Requirements are paramount for supporting the stability of bonded structures, safeguarding versus potential risks, and maintaining the reputation of fabrication firms for supplying top notch products and services.
Secret Components of Welding WPS
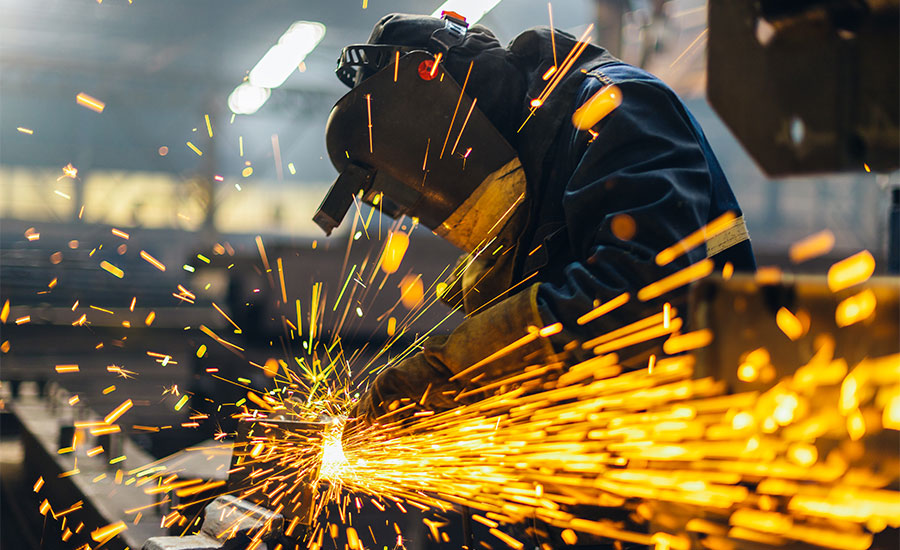
Enhancing Efficiency With WPS
When enhancing welding operations, leveraging the crucial elements detailed in Welding Procedure Specs (WPS) comes to be essential for taking full advantage of and streamlining processes performance. One way to improve performance with WPS is by thoroughly picking the ideal welding criteria. By sticking to the certain standards supplied in the WPS, welders can make sure that the welding devices is established properly, bring about consistent and high-grade welds. In addition, complying with the pre-approved welding sequences detailed in the WPS can click here for more significantly lower the moment invested in each weld, inevitably raising overall performance.
Consistently assessing and updating the WPS to integrate any lessons discovered or technological innovations can likewise contribute to performance enhancements in welding operations. By welcoming the standards set forth in the WPS and continually seeking means to enhance procedures, producers can achieve greater efficiency degrees and superior end outcomes.
Ensuring Safety in Manufacture
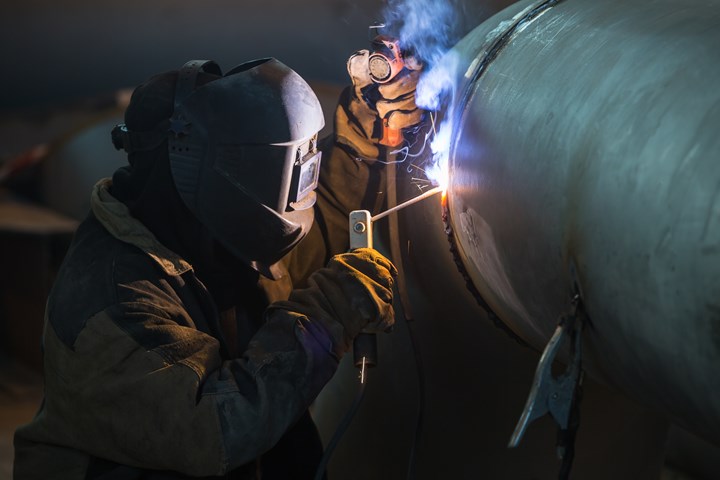
Safety and security methods in manufacture play a pivotal role in safeguarding personnel and optimizing operational procedures. Making certain safety in manufacture includes a complex strategy that encompasses various elements of the welding procedure. One essential aspect is the stipulation of personal safety devices (PPE) tailored to the details threats existing in the manufacture atmosphere. Welders should be outfitted with ideal equipment such as safety helmets, gloves, and safety clothes to minimize risks related to welding tasks.
Additionally, adherence to proper air flow and fume extraction systems is vital in maintaining a healthy work atmosphere. Welding fumes include unsafe compounds that, if breathed in, can pose severe wellness risks. Carrying out effective ventilation procedures helps to lessen exposure to these harmful fumes, advertising respiratory health and wellness amongst workers.
Regular devices upkeep and inspections are likewise vital for making sure safety and security in manufacture. Defective equipment can cause injuries and crashes, underscoring the significance of regular checks and prompt fixings. By focusing on precaution and fostering a society of recognition, manufacture centers can create a protected and efficient job setting for their employees.
Applying WPS Best Practices
To enhance functional efficiency and guarantee high quality results in fabrication processes, integrating Welding Treatment Requirements (WPS) ideal techniques is paramount - welding page WPS. Implementing WPS best techniques entails thorough preparation, adherence to sector requirements, and constant tracking to ensure ideal outcomes. First of all, picking the proper welding process, filler material, and preheat temperature defined in the WPS is critical for attaining the preferred weld high quality. Secondly, ensuring that qualified welders with the necessary certifications carry out the welding procedures according to the WPS standards is necessary for consistency and reliability. Regularly updating and reviewing WPS records to show any procedure enhancements or changes in products is additionally a crucial best technique to preserve accuracy and importance. Furthermore, providing thorough training to welding workers on WPS requirements and ideal methods fosters a society of try here security and high quality within the fabrication setting. By carefully executing WPS best techniques, fabricators can simplify their operations, lessen errors, and supply superior products to satisfy customer expectations.
Conclusion
In conclusion, welding WPS plays a critical duty in ensuring efficiency and safety in manufacture processes. By following these approaches, organizations can open the complete capacity of welding WPS in their construction procedures.
In the world of manufacture, Welding Treatment Specifications (WPS) stand as the backbone of welding procedures, determining the necessary actions for attaining both efficiency and security in the fabrication process. By defining crucial criteria such as welding procedures, products, joint layouts, preheat temperature levels, interpass temperatures, filler metals, and post-weld heat therapy needs, WPS supply a standardized method to welding that enhances performance, top quality, and security in fabrication procedures.
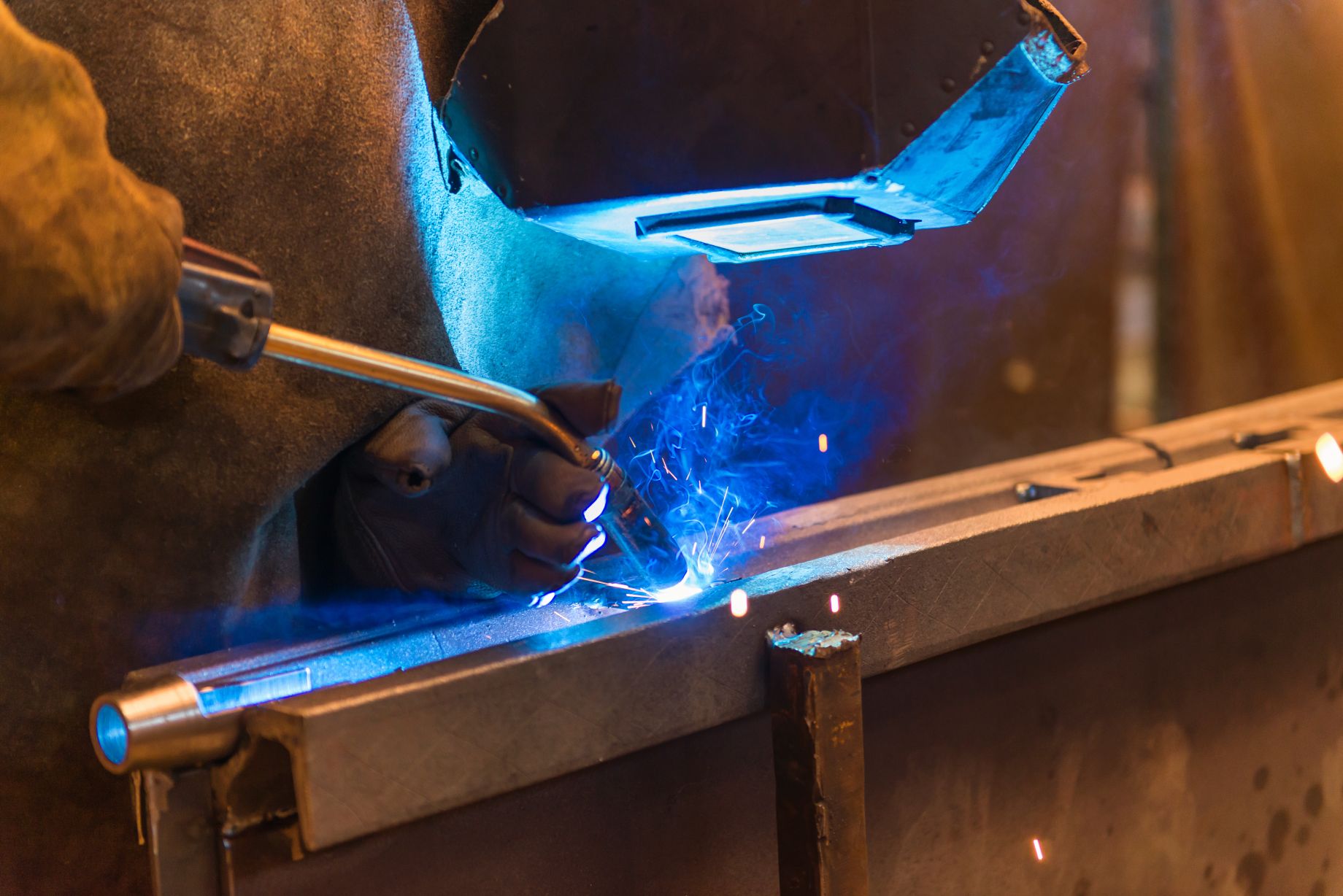
When maximizing welding procedures, leveraging the essential aspects outlined in Welding Treatment Specifications (WPS) becomes necessary for improving procedures and making best use of productivity. (welding WPS)
Report this page